In the world of engineering and machinery, where every component matters, bearings hold a special place. These seemingly small components play a crucial role in enabling smooth and controlled motion, reducing friction, and ensuring efficient energy transfer. However, not all bearings are created equal, and selecting the right one for your application is a critical decision that can impact performance, longevity, and overall efficiency. And when it comes to making that choice, ZNL Bearings is a name you can trust. In this blog, we’ll delve into the art of choosing the right bearing for your application, exploring key factors and considerations that can make all the difference.
Understanding the Basics: Types of Bearings
Before delving into the selection process, it’s essential to have a basic understanding of the different types of bearings available. Bearings can be broadly classified into several categories:
These are the most common type of bearings, utilizing balls to separate the moving parts and reduce friction. They’re suitable for applications with low to moderate loads and moderate speeds.
Roller bearings use spherical,cylindrical or tapered rollers to distribute loads over a larger area. They are often preferred for applications with higher loads and higher speeds.
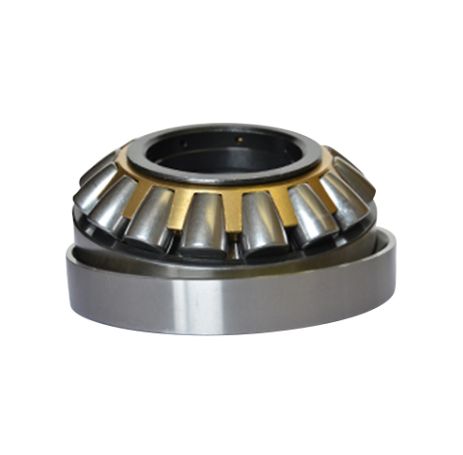
Designed to handle axial loads, thrust bearings are used when the load needs to be supported in one direction only.
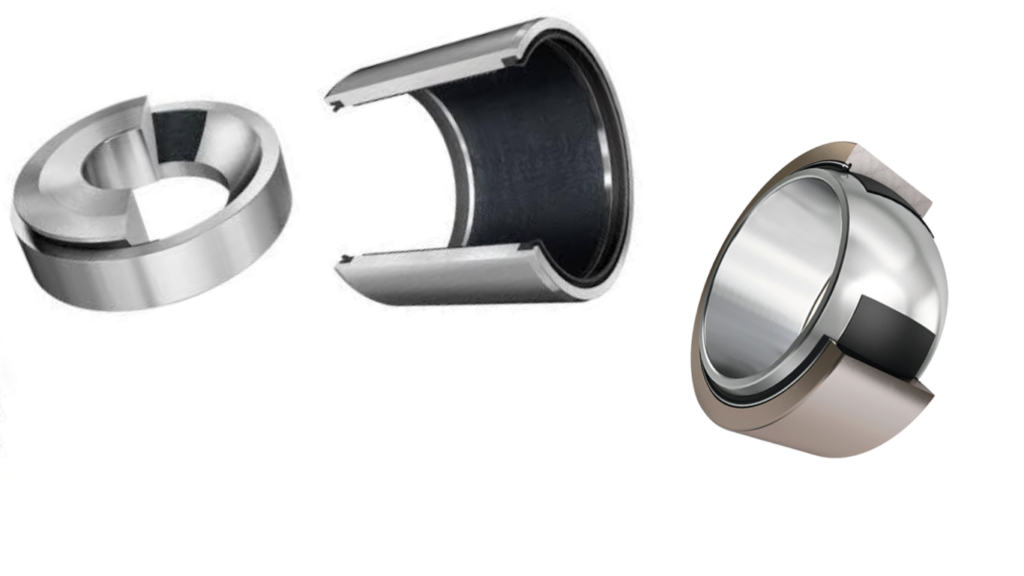
Also known as bushings or sleeve bearings, these involve a sliding motion rather than rolling elements. They’re often used in applications with low speeds and light loads.
Key Factors for Selection:
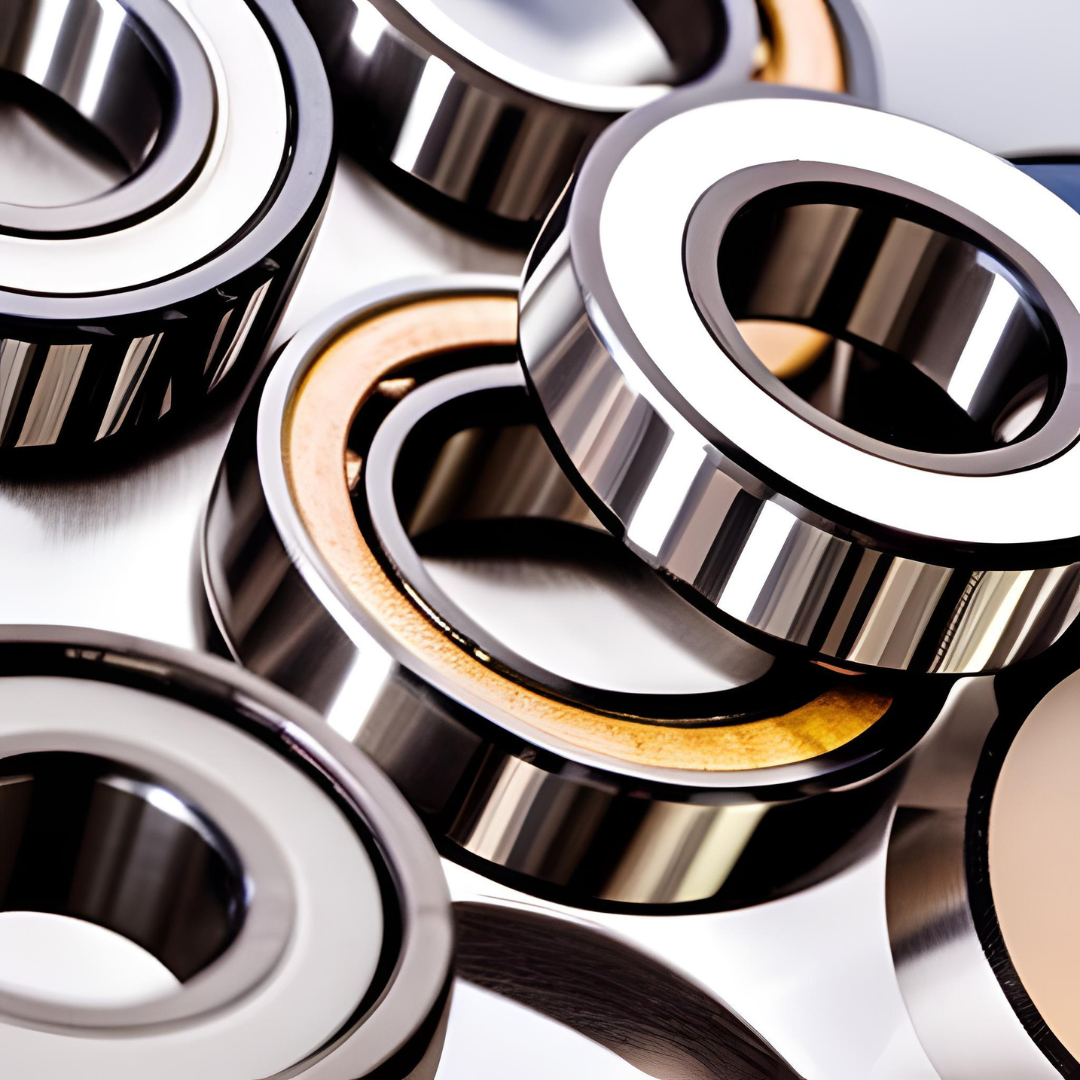
- Load Capacity: One of the most critical factors is determining the load capacity your application requires. Calculate both the radial and axial loads that the bearing will experience to ensure the selected bearing can handle them without premature failure.
- Speed: Consider the rotational speed of the bearing. High-speed applications may require bearings designed to withstand the heat generated at higher RPMs.
- Environment: Assess the operating environment. Is it exposed to dust, moisture, chemicals, or extreme temperatures? Choose bearings with seals or shields that can protect against these elements.
- Precision and Tolerance: Depending on your application’s requirements for accuracy and smoothness, you may need bearings with higher precision and tighter tolerances.
- Size and Fit: Ensure the bearing fits perfectly within your machinery. A proper fit prevents unnecessary stress and premature wear.
- Lubrication: Proper lubrication is essential to reduce friction and wear. Consider whether your application needs lubrication-free or self-lubricating bearings.
- Cost and Longevity: Balance the initial cost of the bearing with its expected lifespan. Sometimes, investing in a higher-quality bearing can lead to long-term savings through reduced maintenance and downtime.
Application-Specific Considerations:
- Automotive Industry: Bearings used in vehicles need to handle a range of conditions, from smooth highways to bumpy terrains. They should be durable, resistant to shock loads, and require minimal maintenance.
- Industrial Machinery: Heavy machinery often requires roller bearings that can handle significant loads and vibrations. Bearings used in conveyor systems, for example, need to be robust and able to handle continuous movement.
- Aerospace and Defense: Bearings used in aerospace applications demand precision and reliability. They must withstand high G-forces, extreme temperatures, and operate flawlessly in critical situations.
- Medical Equipment: Medical devices need precise and often miniature bearings. They should be quiet, smooth, and resistant to corrosion.
- Energy and Power Generation: Bearings used in wind turbines or power plants should be capable of withstanding both high loads and consistent operation over time.
Conclusion: Making the Right Choice with ZNL Bearings
The process of selecting the right bearing for your application involves careful consideration of various factors. With ZNL Bearings as a trusted partner, you’re not just choosing any bearing; you’re choosing precision, reliability, and performance. From load capacity and speed to environmental conditions and the specific demands of your industry, ZNL Bearings offers a range of solutions designed to excel in diverse applications. A well-chosen bearing can extend the lifespan of your machinery, enhance performance, and reduce maintenance costs.
In the world of machinery and engineering, choosing the right bearing isn’t just a decision; it’s an investment in the reliability and efficiency of your application. So, take the time to evaluate your needs, consider all the factors, and partner with reputable bearing manufacturers to ensure your machinery operates at its best, driven by the precision and performance of the perfect bearing choice.