The injection moulding industry plays a critical role in the global manufacturing sector, particularly in producing high-quality plastic parts used in various industries, including automotive, electronics, healthcare, and consumer goods. As injection moulding machines are required to operate with precision and efficiency, the need for reliable components becomes essential. One such component is the bearing, which ensures smooth rotational movements, reduces friction, and handles the mechanical stresses encountered during operation.
Bearings, especially Spherical Roller Bearings and Tapered Roller Bearings, play a pivotal role in enhancing the operational efficiency and durability of injection moulding machines. ZNL Bearings, a trusted name in the industry, offers these high-performance bearings, specifically designed to meet the demanding requirements of injection moulding processes.
In this blog, we will explore the importance of bearings in the injection moulding industry and highlight how Spherical Roller Bearings and Tapered Roller Bearings from ZNL Bearings help ensure reliable and efficient performance in this high-stakes environment.
Importance of Bearings in Injection Moulding Machines
Injection moulding machines are complex systems that involve high-speed, high-pressure operations. These machines rely on several critical components, including bearings, to ensure smooth functioning. Bearings play the following key roles in the operation of an injection moulding machine:
- Reducing Friction: Bearings minimize friction between rotating components, ensuring smooth operation and reducing wear and tear on the machine’s parts. This extends the life of the machine and reduces maintenance costs.
- Supporting High Loads: Injection moulding machines experience significant radial and axial loads during operation. Bearings are responsible for supporting these loads, ensuring that the machine can handle high-pressure injection processes without failure.
- Precision and Accuracy: Bearings ensure that the movements of machine components are precise and accurate. This is crucial in the injection moulding process, where even minor misalignments can lead to defects in the final product.
- Energy Efficiency: By reducing friction and allowing for smoother operation, bearings help improve the energy efficiency of injection moulding machines. This leads to reduced energy consumption and operating costs for manufacturers.
Given these roles, it is clear that bearings are essential to the efficiency, reliability, and longevity of injection moulding machines. ZNL Bearings, with its expertise in manufacturing high-quality bearings, offers specialized solutions for the injection moulding industry, particularly in the form of Spherical Roller Bearings and Tapered Roller Bearings.
Spherical Roller Bearings: Enhancing Durability and Misalignment Tolerance
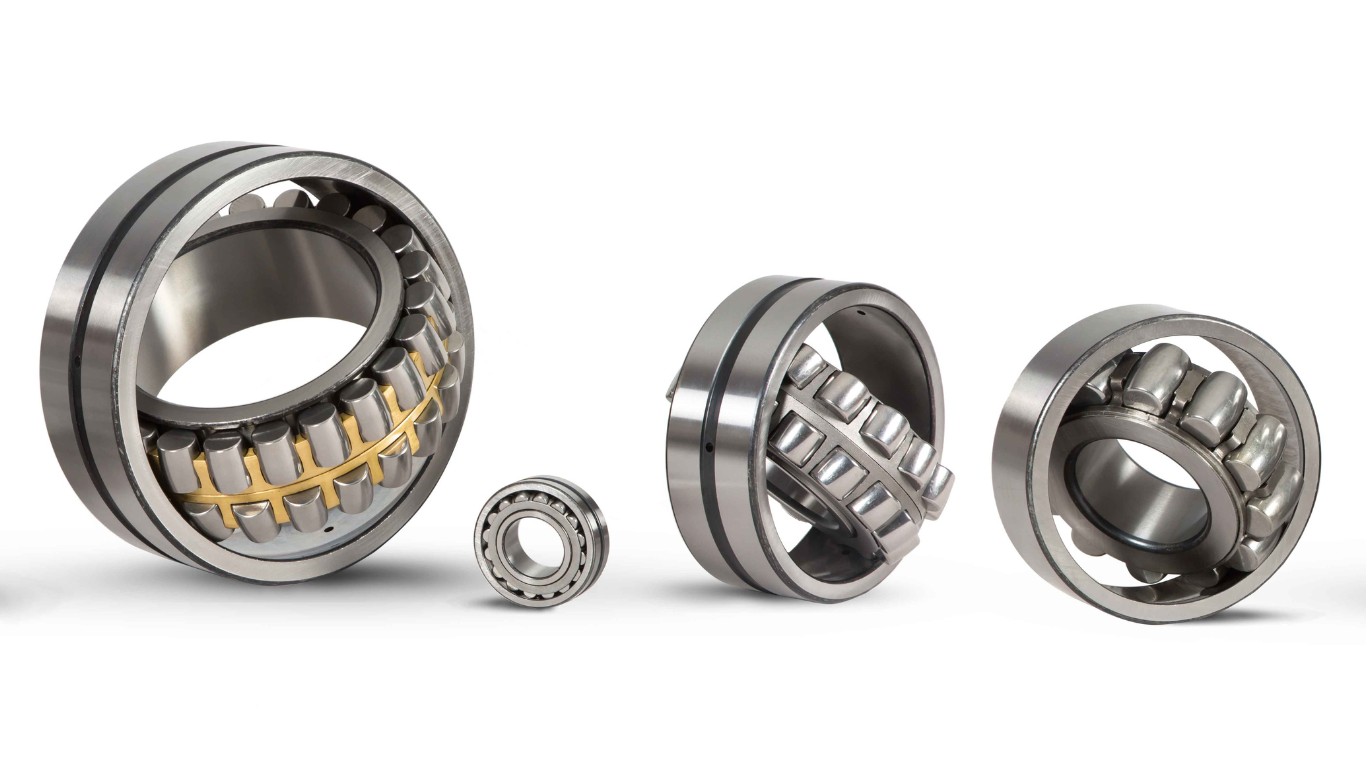
Spherical Roller Bearings from ZNL Bearings are a top choice for the injection moulding industry due to their ability to handle both radial and axial loads. This makes them ideal for machines that experience heavy loads during operation.
Key Benefits of Spherical Roller Bearings in Injection Moulding:
- Handling High Loads: Spherical Roller Bearings are designed to accommodate heavy radial loads and moderate axial loads. In injection moulding machines, where high-pressure injections occur, these bearings ensure that the machine can handle these stresses without compromising performance.
- Misalignment Tolerance: A key advantage of Spherical Roller Bearings is their capacity to handle misalignment effortlessly. In injection moulding machines, misalignment between the shaft and housing can occur due to heavy loads or structural deformations. Spherical Roller Bearings can automatically compensate for these misalignments, ensuring smooth operation and preventing machine downtime.
- Shock Load Resistance: Injection moulding processes often involve sudden, high-pressure injections, which can cause shock loads on the machine’s components. Spherical Roller Bearings are highly resistant to shock loads, providing an extra layer of protection for the machine’s mechanical parts.
- Extended Service Life: Thanks to their robust design and ability to handle extreme operating conditions, Spherical Roller Bearings from ZNL offer an extended service life. This reduces the need for frequent bearing replacements and minimizes maintenance costs for manufacturers.
- Low Friction and Energy Efficiency: Spherical Roller Bearings are designed to operate with low friction, reducing the overall energy consumption of the injection moulding machine. This results in streamlined production processes and significant savings for manufacturers.
By incorporating ZNL’s Spherical Roller Bearings into their injection moulding machines, manufacturers can benefit from increased machine reliability, reduced downtime, and improved production efficiency.
Tapered Roller Bearings: Precision and Load Distribution
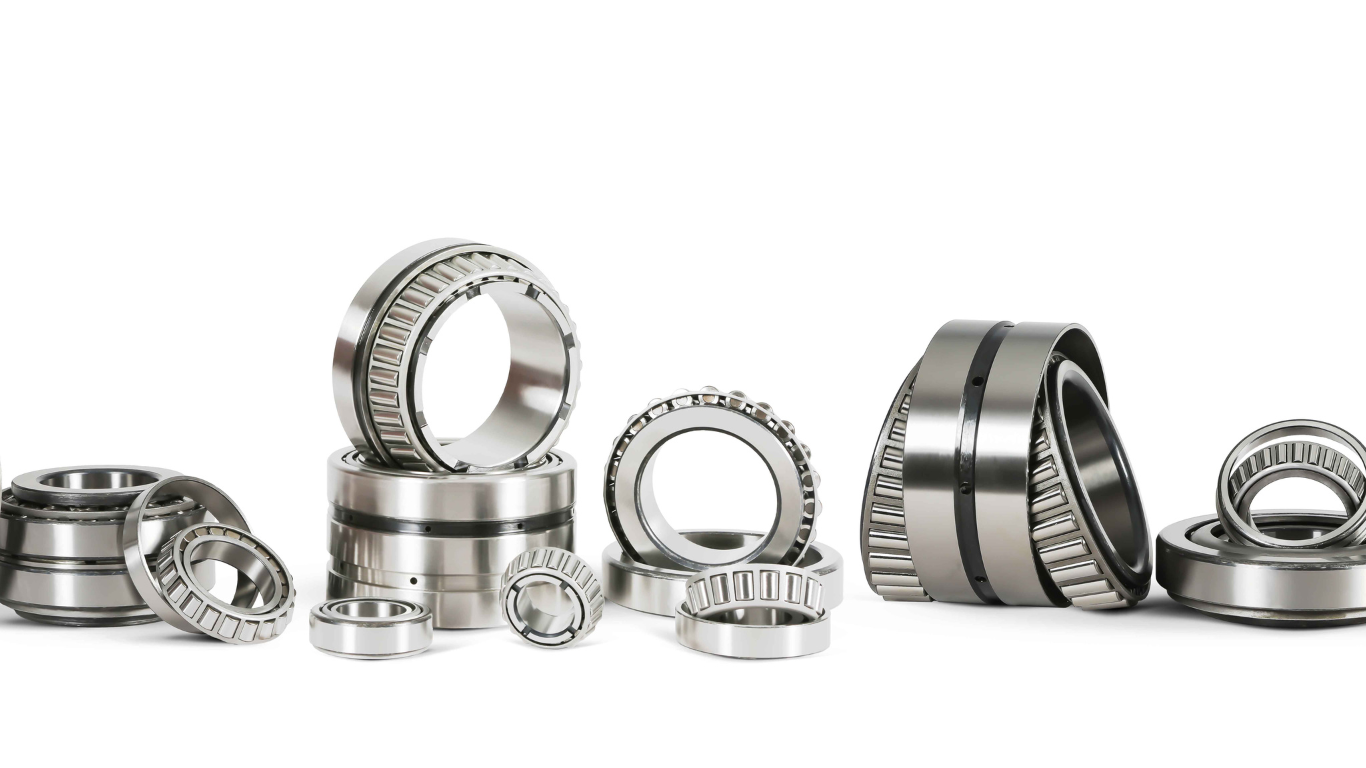
Another essential bearing type used in the injection moulding industry is the Tapered Roller Bearing. ZNL Bearings offers high-quality Tapered Roller Bearings that are specifically designed to handle both radial and axial loads, making them ideal for use in high-stress applications such as injection moulding.
Key Benefits of Tapered Roller Bearings in Injection Moulding:
- Excellent Load Distribution: Tapered Roller Bearings are designed to distribute loads evenly across the bearing surface. This ensures that the bearing can handle both radial and axial loads without causing excessive wear on the machine’s components.
- High Precision: Tapered Roller Bearings offer high precision, which is critical in the injection moulding process. These bearings ensure that the machine’s components rotate smoothly and accurately, resulting in high-quality moulded products with minimal defects.
- Durability under High Stress: Injection moulding machines operate under high stress, particularly during the injection phase. Tapered Roller Bearings are known for their ability to withstand high axial and radial loads, making them ideal for the demanding conditions of injection moulding processes.
- Reduced Maintenance Requirements: Like Spherical Roller Bearings, Tapered Roller Bearings from ZNL are designed for durability and extended service life. This reduces the need for frequent maintenance and bearing replacements, allowing manufacturers to focus on maximizing production output.
- Versatility: Tapered Roller Bearings are versatile and can be used in various parts of the injection moulding machine, including the clamping unit and injection unit. This flexibility makes them an ideal choice for manufacturers looking for a bearing solution that can meet a wide range of operational requirements.
By using ZNL’s Tapered Roller Bearings, injection moulding machine manufacturers can ensure that their machines operate with precision, reliability, and efficiency, even under high loads and demanding conditions.
Conclusion
The role of bearings in the injection moulding industry cannot be overstated. Bearings are essential components that ensure smooth operation, precision, and durability in injection moulding machines. Spherical Roller Bearings and Tapered Roller Bearings from ZNL Bearings provide the necessary performance characteristics to meet the demands of the injection moulding process.
By incorporating ZNL Bearings‘ products into their machines, manufacturers can benefit from improved machine reliability, reduced downtime, and enhanced production efficiency. With a focus on quality and innovation, ZNL Bearings is a trusted partner for businesses in the injection moulding industry, helping them achieve superior performance and long-term success.
For more information on ZNL Bearings and our range of products for the injection moulding industry, visit our website or contact our team of experts today.