Data is important for reasoning and enhancing activities in large-scale manufacturing. It is particularly relevant in bearing manufacturing factories as number of machines have to run on maximum efficiency, effectiveness and power. This calls for a robust management system for this kind of industry where a factory can be so expansive with whatever machine you can name. Data Acquisition System (DAQ) can greatly improve plant management if machinery performs with maximum efficiency and accuracy on the other hand.Basically, a Data Acquisition System (DAQ) has the capacity of improving plant management by ensuring that the machines run efficiently and precisely. The function of the DAQ is to look at all machine parameters as well as their statuses in any given plant. Consistent surveillance of vital plant sections has been particularly important in ensuring uninterrupted operation and avoiding critical occurrences at the same time as it has assisted in the prevention of such incidents. In this blog, ZNL Bearings will shed light on the role, importance and principles of DAQ system in plant operations.
Understanding Principles Of A Data Acquisition System
A Data Acquisition System (DAQ) is an instrument which transforms physical parameters to digital data that can be read by a computer. They are crucial for plant operations, in particular monitoring and controlling processes and asset management as well as performance optimization. Normally, this system comprises sensors, DAQ devices and software.
Key Elements Of Data Acquisition System:
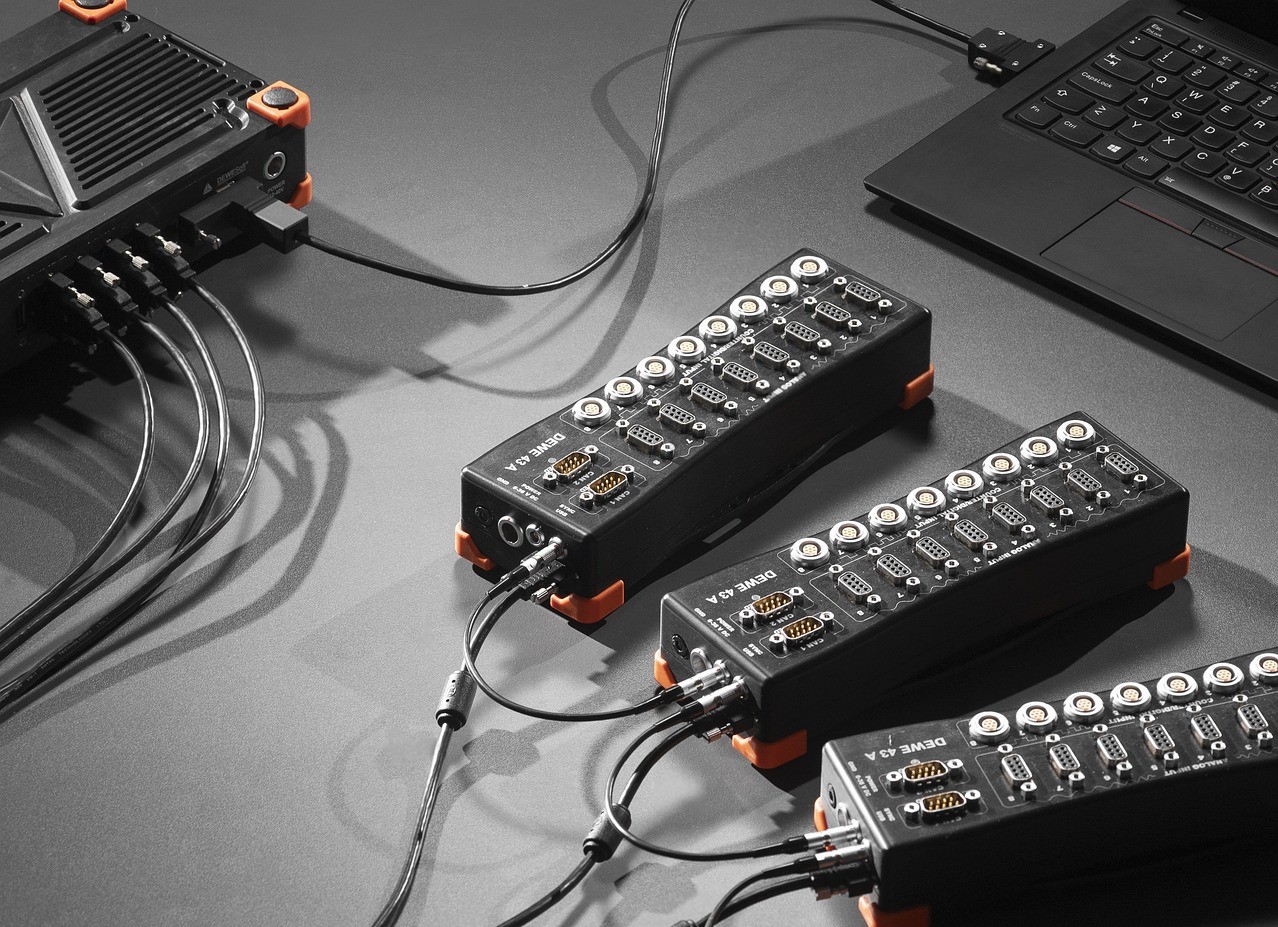
Sensors: Sensors are devices which convert physical parameters into an electrical signal that can be measured or recorded. Sensors measure temperature, pressure, flow rate and level among others. They can also alert the users of possible machine breakage before it occurs by sensing vibration or acoustics with high frequency.
Signal Conditioning Circuitry: Signal conditioners enhance, filter, and modify sensor signals, so that data acquisition hardware can read them. If the signal conditioner sensed from the transducer may not directly be suitable for DAQ hardware, this device is required to make it readable. Such conditioners also make it possible to isolate and shield against high transient voltages, thereby increasing system dependability.
Analog-to-Digital Converter (ADC)
Converts the conditioned sensor signals into digital values.
Computer with DAQ Software
Utilized for data logging and analysis. Popular software packages include Matlab, FlexPro, imc STUDIO, and imc FAMOS.
Hardware: The hardware includes the physical components on which the system runs for acquiring data like sensors, signal conditioners, data acquisition cards, and associated cabling. This serves as an intermediary between computers and sensors with provision for input as well as output. Data analysis in real-time becomes possible when high-speed multiple channel supporting cards are annexed onto this acquisition card of high performance.
Software: DAQ software provides a user interface for configuring and controlling data acquisition devices and for viewing and analyzing the acquired data. Advanced DAQ software like LabVIEW includes features like real-time data visualization, automated reporting, and integration with other enterprise systems such as SCADA (Supervisory Control and Data Acquisition) and ERP (Enterprise Resource Planning).
The Vital Role of DAQ Systems in Plant Operations
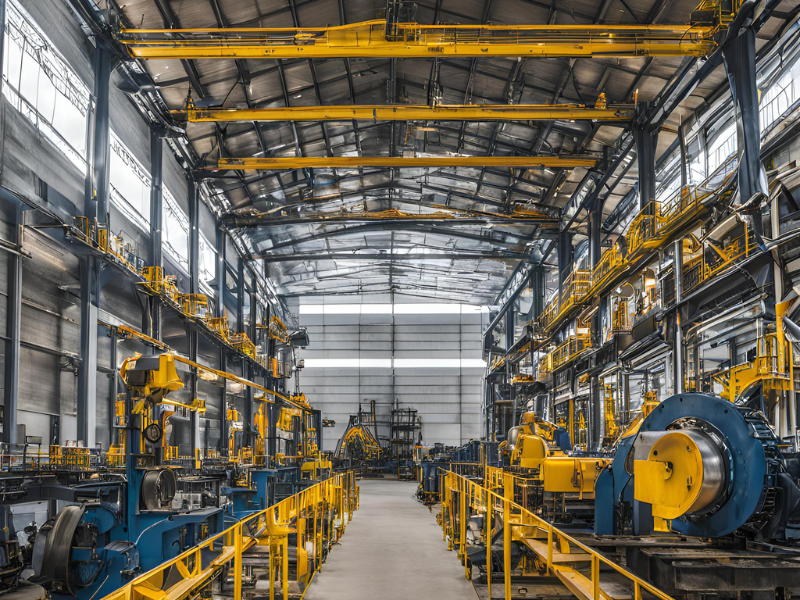
A Data Acquisition System offers numerous benefits, ensuring a smooth workflow and efficient operations while aiding in better decision-making. Here are some reasons why a DAQ system is crucial for plant operations:
Improved Efficiency: DAQ systems can enhance the efficiency of plant operations by delivering accurate and timely data regarding processes and equipment. This information can be used to optimize production, address issues, and improve safety and environmental performance. For example, real-time monitoring of critical parameters can prevent bottlenecks and streamline workflows.
Cost Optimization: DAQ systems help reduce downtime, improve quality and production, and save energy and resources. They assist in identifying opportunities for cost savings and process improvements. Predictive maintenance, enabled by DAQ systems, can significantly reduce maintenance costs by addressing issues before they lead to costly failures.
Monitoring Machinery Usage: Tracking the usage and operational time of machinery is critical for assessing utilization rates and aligning them with energy-related aspects. Detailed usage reports can help in scheduling machinery operation during off-peak energy hours, reducing energy costs.
Identifying Areas for Improvement: By gathering data on various facets of plant operations, such as production rates, energy consumption, and equipment performance, DAQ systems can pinpoint areas needing improvement. Analyzing historical data trends can uncover inefficiencies and guide process enhancements.
Enhanced Decision Making: Data collected by DAQ systems aids in making informed decisions about future operations, such as scheduling maintenance or altering production processes. The integration of DAQ systems with machine learning algorithms can provide predictive insights, further enhancing decision-making capabilities.
Facilitating Process Automation: DAQ systems prepare manufacturing plants for industrial automation, which can accelerate the organization’s profitability in various ways. Automated control systems can respond to DAQ data in real-time, adjusting operations to maintain optimal conditions.
Preventive Maintenance: DAQ systems ensure timely and preventive maintenance, increasing machinery lifespan and preventing breakdowns. By monitoring wear and tear indicators, DAQ systems can schedule maintenance activities during planned downtimes, minimizing operational disruptions.
Ensuring Compliance: DAQ systems can help manufacturing plants comply with regulatory requirements by providing accurate and verifiable data on process conditions. This is particularly important in industries with stringent safety and environmental regulations.
Quality Control: DAQ systems play a vital role in quality control by continuously monitoring product quality parameters. Immediate detection of deviations ensures corrective actions are taken promptly, maintaining high product standards.
Enhancing Operational Efficiency with Digital Integration
While plant operations can be manually managed, transitioning to a digital system like DAQ offers numerous benefits. DAQ eliminates the errors associated with manual inspection and checking, ensuring plant operations run smoothly within safety norms, conserving resources, and reducing costs. With DAQ, plant performance can be highly optimized, tracking the entire manufacturing process to ensure seamless operations without any red flags. Implementing DAQ systems not only enhances operational efficiency but also positions plants for future advancements in industrial automation and smart manufacturing technologies.