Bearing manufacturing and inspection are vital processes in the world of mechanical engineering, ensuring the reliable performance of machines across various industries. ZNL Bearings, a reputable name in the field, has been pioneering innovation and precision in bearing production for years. In this blog, we will delve into the fascinating process of bearing manufacturing and the critical role that inspection plays in maintaining quality and reliability.
I. The Foundation: Raw Material Selection
The journey of a bearing begins with the careful selection of high-quality raw materials. Typically, bearing components are crafted from various materials, including steel, brass, and even plastic. Steel is a popular choice for most applications due to its excellent strength, durability, and heat resistance. ZNL Bearings meticulously selects the appropriate steel alloy, ensuring it meets the required metallurgical standards.
II. Forging: Shaping the Precursor
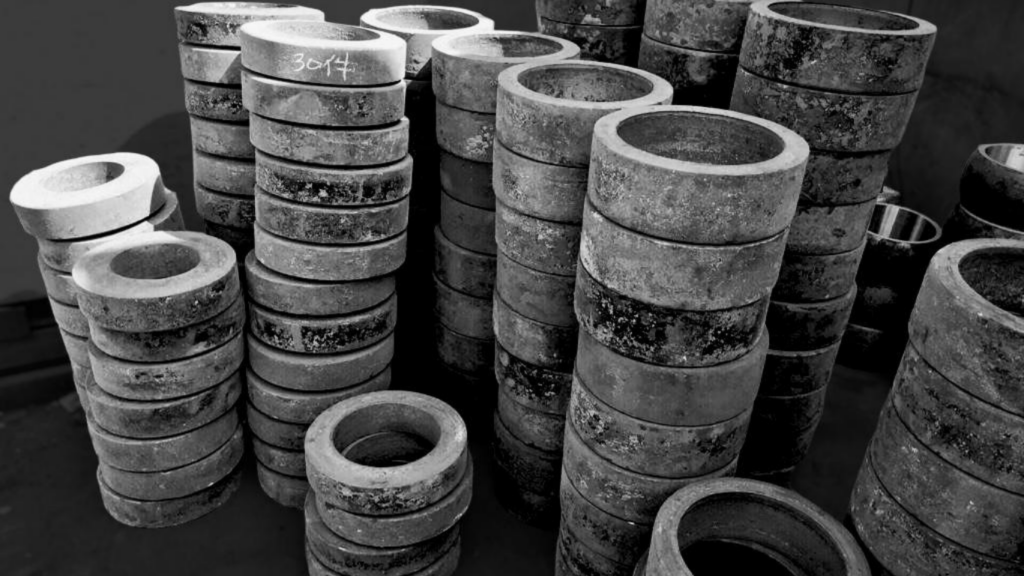
The next step involves forging, where the selected steel alloy is heated and then shaped into a precursor for the bearing ring. This process is essential to achieve the desired dimensions and physical properties. Precise forging ensures the strength and integrity of the bearing.
III. Turning and Machining: Precision in Action
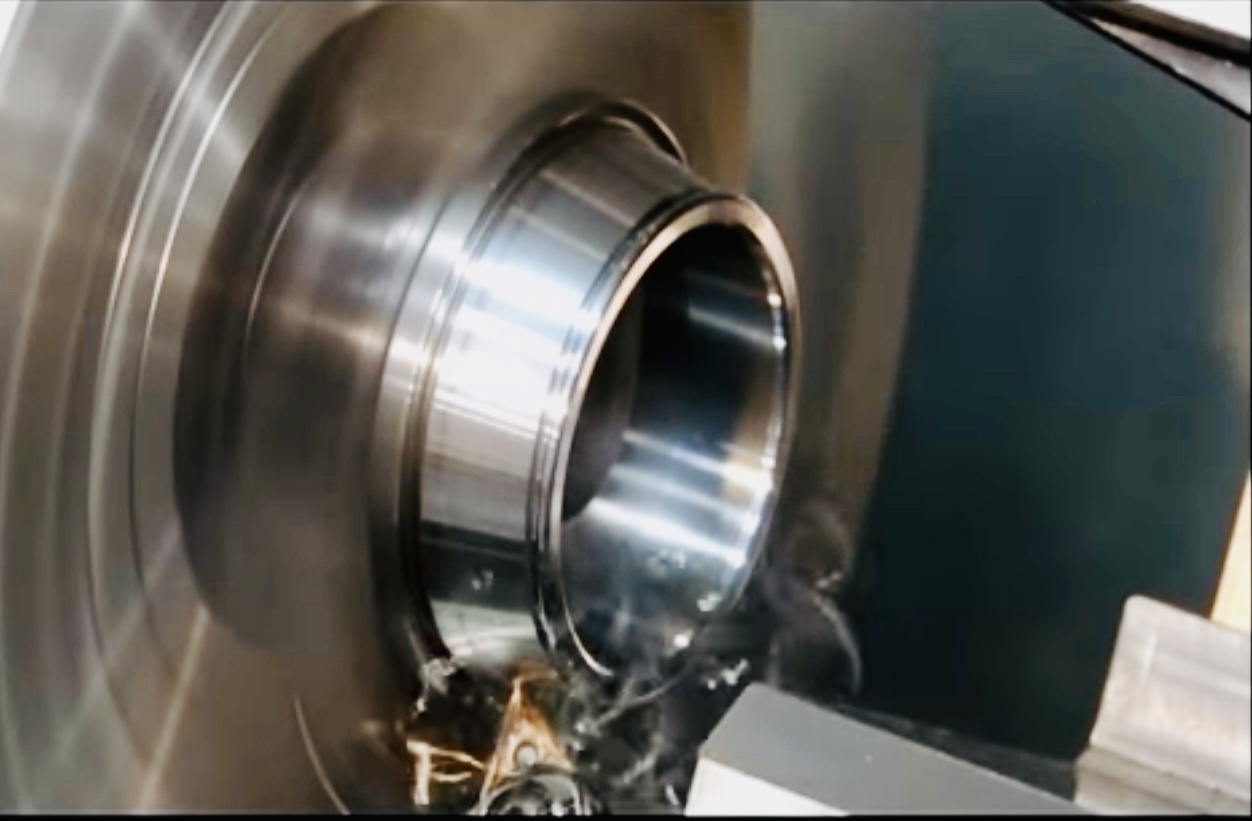
After forging, the precursor goes through turning and machining processes. In turning, the outer and inner diameters of the rings are precisely shaped. These components must meet tight tolerances to ensure that the bearing functions optimally. Advanced CNC machines at ZNL Bearings enable exceptional accuracy during the turning and machining phases.
IV. Heat Treatment: Enhancing Strength
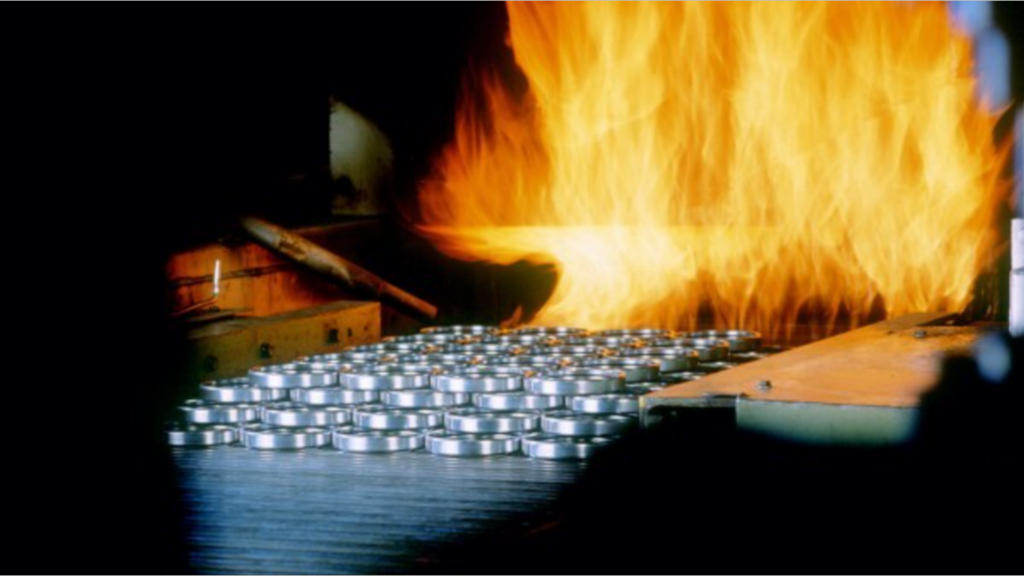
Heat treatment is a critical step in bearing manufacturing. The rings undergo processes like quenching and tempering to enhance their mechanical properties, including hardness and durability. Achieving the right balance in hardness is crucial to withstand the forces and stresses the bearing will encounter during operation.
V. Grinding: Achieving Superb Precision
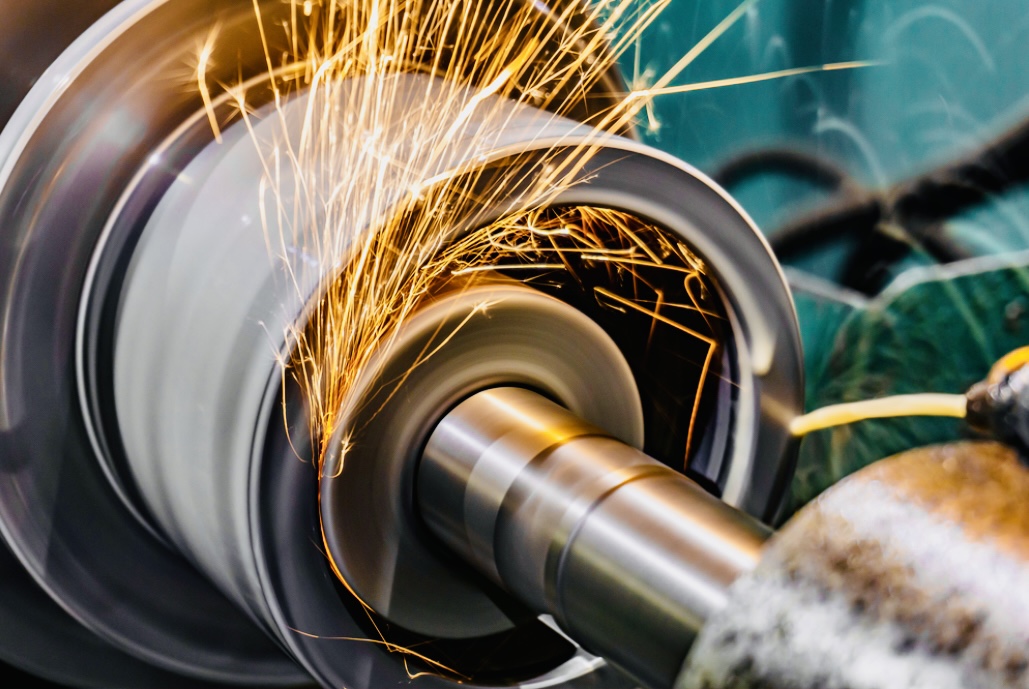
Grinding is perhaps the most crucial stage in bearing manufacturing. It is the process where the ring’s outer and inner diameters are ground to incredibly tight tolerances, ensuring the desired shape, surface finish, and fit. This precision is vital to minimize friction and maintain bearing longevity.
VI. Assembly: Bringing It All Together
After grinding, the bearing’s various components – the inner ring, the outer ring, the rolling elements, and the cage – are assembled. During this stage, precision is once again paramount, ensuring that all parts fit together seamlessly. Proper assembly guarantees the bearing’s ability to handle radial and axial loads efficiently.
VII. Lubrication: The Lifeblood of Bearings
Lubrication is essential to reduce friction and wear within the bearing, enhancing its lifespan. ZNL Bearings pays close attention to selecting the right lubricants based on the application and operating conditions. The right lubrication ensures smooth rotation and minimizes wear and tear.
VIII. Inspection: Ensuring Quality
Bearing inspection is a critical aspect of the manufacturing process. ZNL Bearings employs a comprehensive approach to quality control to guarantee that every bearing meets the highest standards.
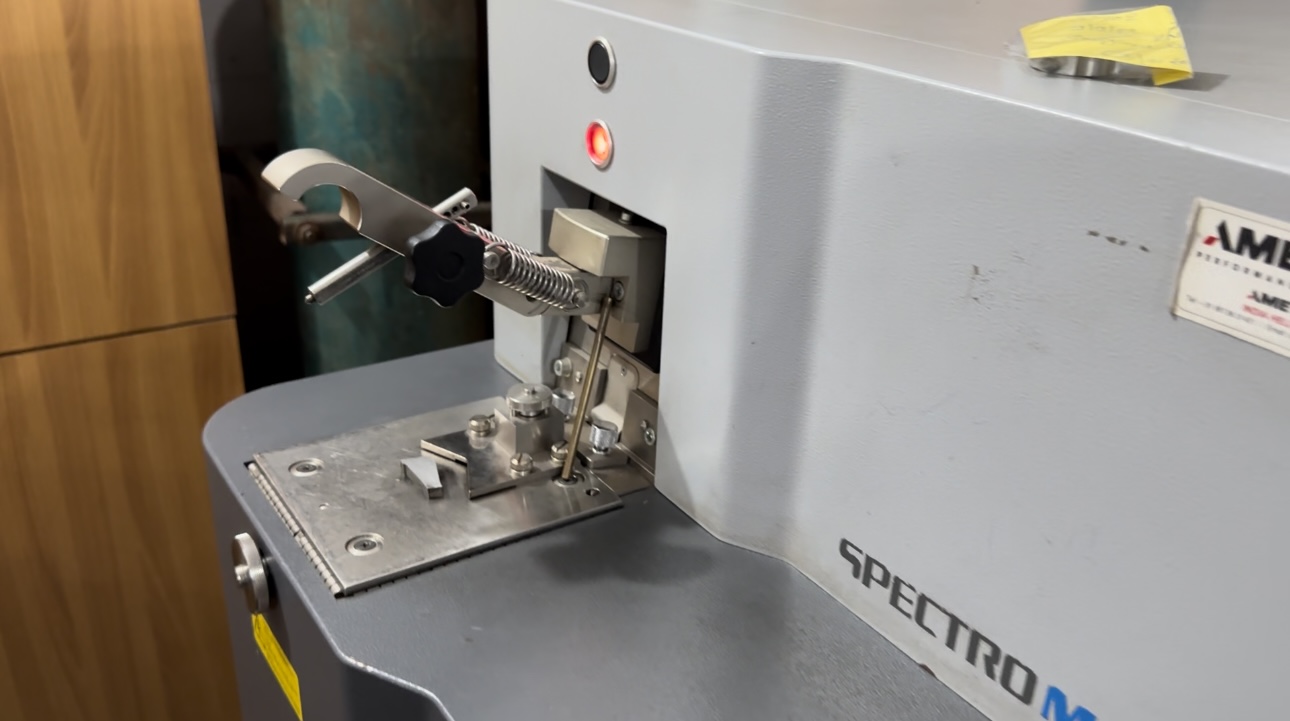
Dimensional Inspection: This checks the bearing’s critical dimensions and tolerances. Any deviations from the specified measurements are addressed to maintain precision.
Visual Inspection: Visual checks are performed to identify any visible defects or surface irregularities. These could be signs of damage during the manufacturing process or issues with the raw materials.
Material Analysis: Using advanced techniques like spectrometry, the material composition of the bearing is analyzed to ensure it matches the required specifications.
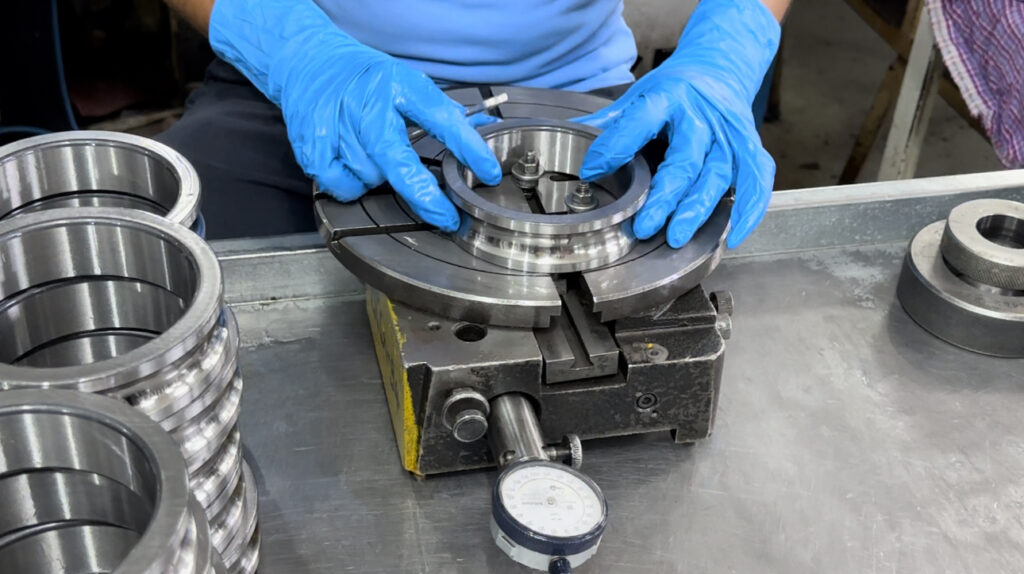
Hardness Testing: The hardness of the bearing’s surfaces is carefully examined. Deviations from the desired hardness could affect its performance and longevity.
Friction Testing: Testing is done to ensure the bearing’s friction and resistance meet the required specifications. This is crucial for optimal performance in various applications.
Noise and Vibration Testing: These tests assess the bearing’s noise and vibration levels, ensuring that it operates smoothly and quietly, a crucial factor in many applications.
Endurance Testing: Bearings may undergo extensive testing under challenging conditions to assess their long-term performance.
Final Visual Inspection: A final visual inspection is conducted to ensure that the bearing is free from any surface defects or anomalies.
IX. Packaging and Shipment: Ready for Service
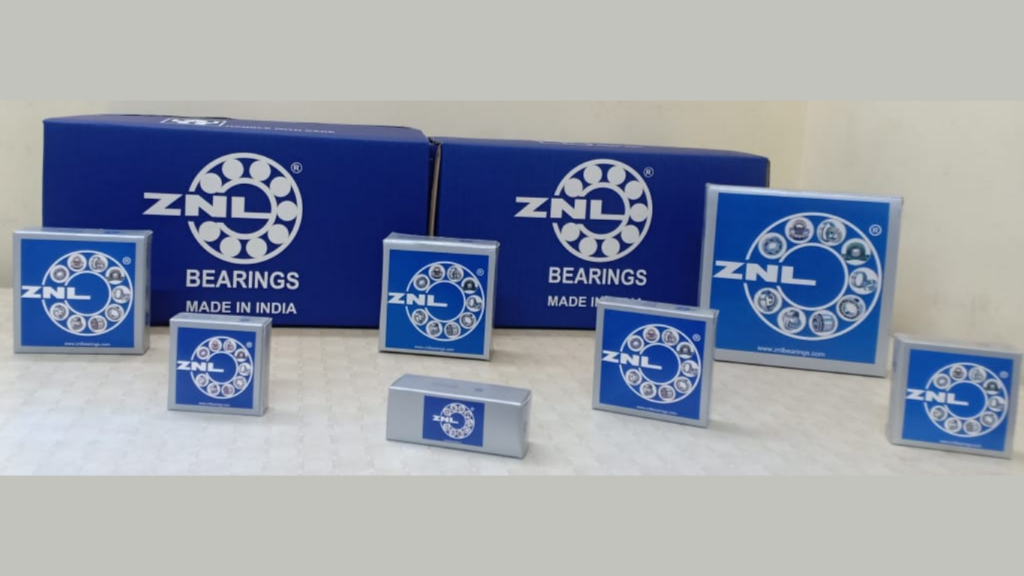
Once bearings have successfully passed the rigorous inspection process, they are carefully packaged and prepared for shipment to customers. ZNL Bearings ensures that the bearings are packaged securely to prevent any damage during transport.
Conclusion
Bearing manufacturing is a complex and fascinating process that involves a series of intricate steps, from selecting the right raw materials to precision machining, inspection, and quality control. ZNL Bearings, with its dedication to quality and innovation, stands at the forefront of this industry, producing reliable and efficient bearings for various applications. Through careful engineering and meticulous inspection, they provide customers with the assurance of robust and dependable bearings for a multitude of uses. The art of bearing manufacturing and inspection is a testament to human ingenuity and technology, and it continues to drive progress and reliability in the world of machinery.