The manufacturing landscape has been evolving at a remarkable pace, and one of the most significant advancements in recent years is 3D printing, also known as additive manufacturing. This technology has revolutionized various industries by enabling the creation of complex, custom components with unprecedented speed and precision. In the world of bearing manufacturing, 3D printing holds the potential to be a game changer, especially when it comes to customization. While ZNL Bearings is not currently using 3D printing technology, we recognize the immense possibilities it offers and are dedicated to exploring the innovations that can benefit our clients in industries such as thermal power, agriculture, cement, and more.
The Rise of 3D Printing in Manufacturing
3D printing has become a highly valuable tool in industries where precision and customization are paramount. In traditional manufacturing processes, creating custom bearings, especially for unique or low-volume applications, often involves lengthy lead times and significant costs. This is where 3D printing can make a notable difference.
With 3D printing, manufacturers can produce custom-designed bearings faster and with greater flexibility, allowing for the creation of parts that are tailored to specific applications. For example, in industries like thermal power plants, agricultural machinery, and cement production, where specialized bearings are often needed, 3D printing can enable quick adjustments to design specifications, reducing downtime and improving operational efficiency.
At ZNL Bearings, we understand the importance of offering custom solutions for various industries. While we currently excel in providing high-quality bearings, including tapered roller bearings, spherical roller bearings, and cylindrical roller bearings, the potential of 3D printing for future customization is undeniable.
How 3D Printing Enhances Customisation in Bearing Manufacturing

The key advantage of 3D printing in bearing manufacturing lies in its ability to produce complex geometries and bespoke components with a high level of accuracy. Traditional manufacturing methods, such as machining or casting, are often limited in their ability to create intricate designs, and any modification requires expensive retooling.
However, with 3D printing, the design process is far more flexible. Bearings can be created with specific dimensions, material properties, and performance characteristics tailored to the unique requirements of an application. For example, in industrial gearboxes or pumps, where precision is essential, 3D-printed bearings could be designed to withstand specific load capacities, rotational speeds, or environmental conditions, ensuring optimal performance and extended lifespan.
At ZNL Bearings, we specialize in delivering durable and reliable bearing solutions for industries like the paper industry, cement plants, and automotive manufacturing, and while we do not currently use 3D printing, we are constantly looking to enhance our offering with innovative techniques. The possibilities for customization with 3D printing could provide even more tailored solutions for these demanding applications.
Material Flexibility and Durability
Another area where 3D printing shines in bearing manufacturing is material flexibility. With traditional manufacturing, materials like steel, ceramic, and polymers are used for bearings, but each material comes with its own set of limitations in terms of shape, weight, and durability. 3D printing, on the other hand, allows for the use of composite materials that can combine the benefits of different substances, such as strength and lightweight properties.
Imagine being able to customize a bearing for an agricultural machine that requires extra resilience against dust and debris, or creating a high-precision bearing for an automotive engine that needs to perform at high temperatures. With 3D printing, engineers can test new materials and even produce prototypes rapidly, making it easier to find the right combination for any specific application.
ZNL Bearings prides itself on delivering the highest quality products, including deep groove ball bearings and angular contact bearings, to industries like thermal power plants and industrial machinery. As 3D printing technology advances, we see a future where this technology may allow us to develop even more innovative material combinations and structures to enhance the performance and longevity of our bearings.
Cost Efficiency and Time Savings
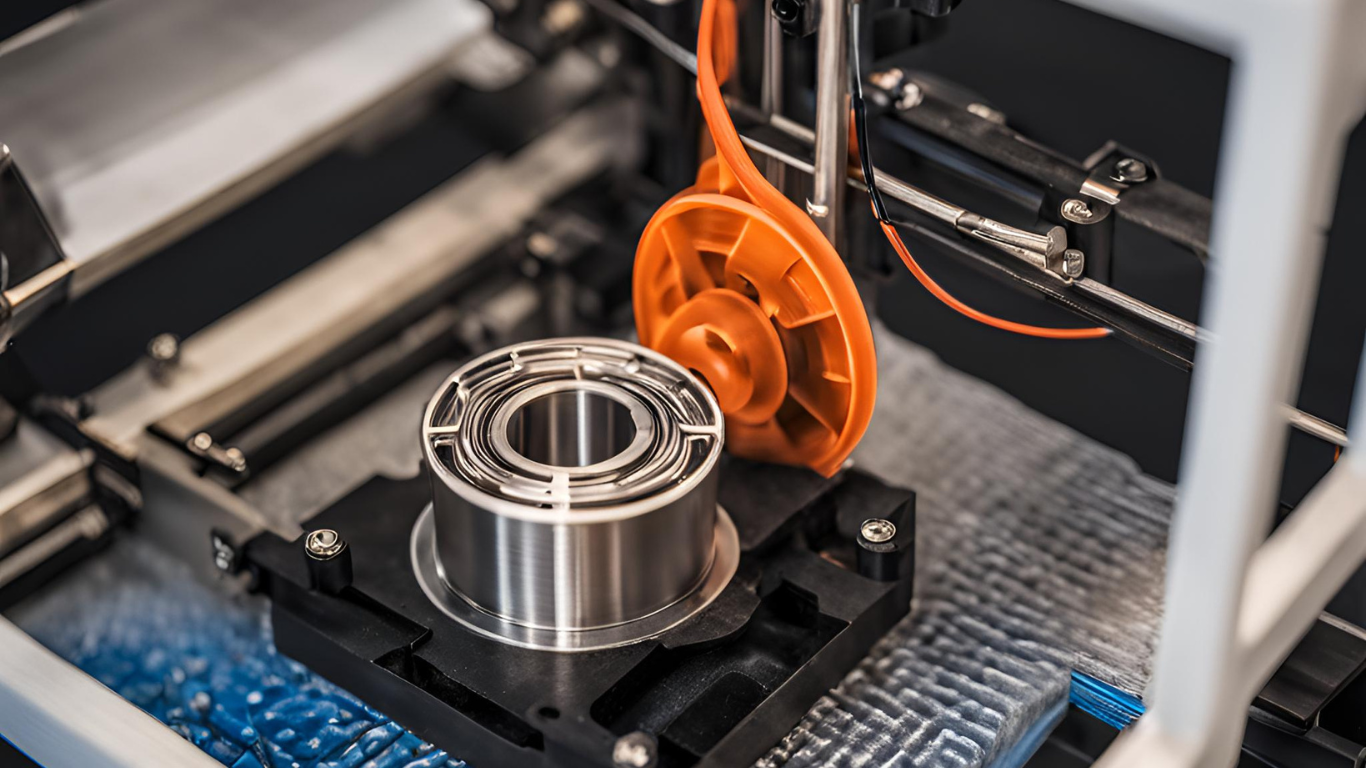
In traditional manufacturing, creating a custom bearing often involves creating a mold, which is both time-consuming and expensive, particularly for small batches or one-off orders. 3D printing eliminates the need for molds, allowing manufacturers to produce bearings on demand, cutting down lead times, and reducing overall production costs.
This is particularly beneficial for industries that require specialized bearings for short-term projects or unique machines, such as cement plants or paper manufacturing, where custom components may not always be available off the shelf. By using 3D printing, manufacturers can reduce the time between design and deployment, ensuring that operations are not hindered by long waiting periods for parts.
While ZNL Bearings currently excels in producing tapered roller bearings, spherical roller bearings, and cylindrical roller bearings for high-demand industries, the speed and efficiency of 3D printing offer a glimpse into the future of manufacturing, where custom parts can be produced quickly and cost-effectively.
The Future of 3D Printing in Bearing Manufacturing
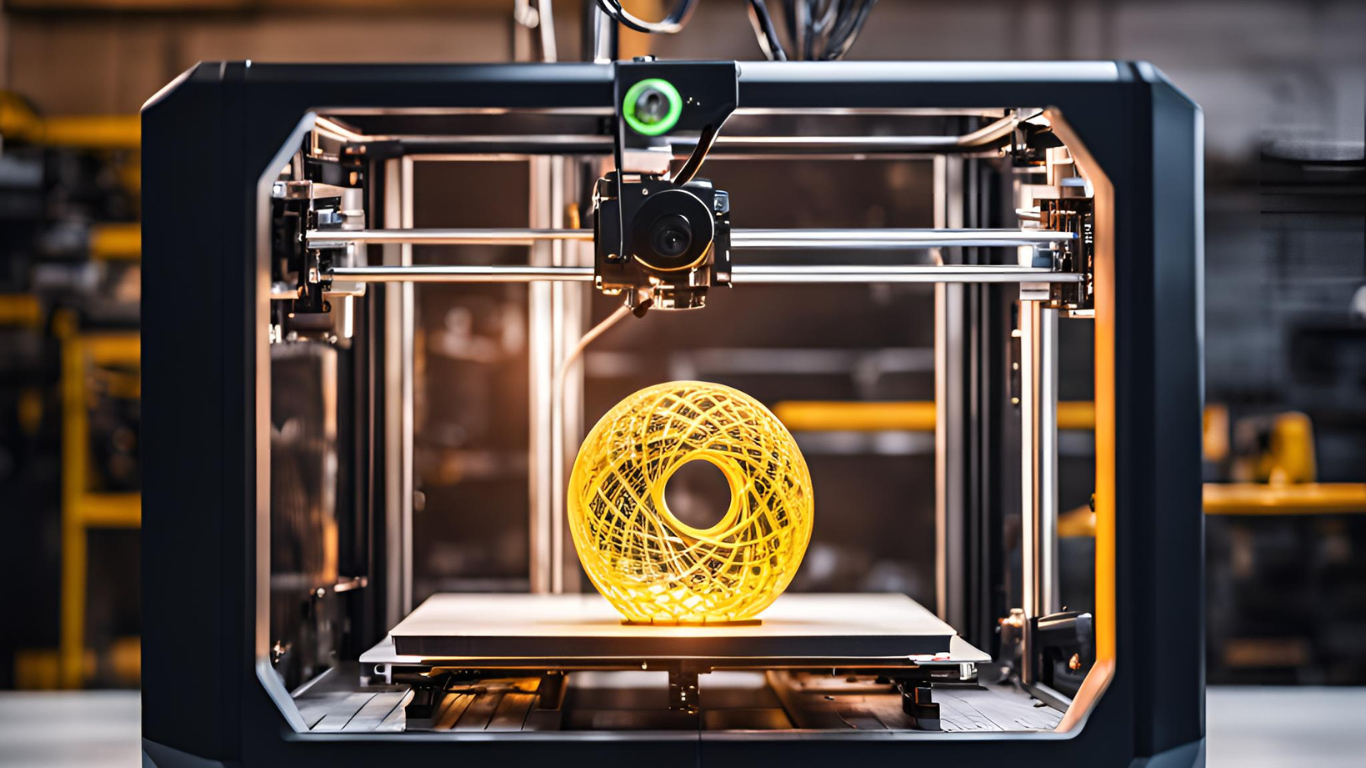
While ZNL Bearings does not yet employ 3D printing technology in our production processes, we are always on the lookout for emerging technologies that can improve the quality and customization of our products. The potential for 3D printing in bearing manufacturing is enormous, and as the technology continues to mature, it may well become a vital tool in delivering custom solutions to industries ranging from thermal power plants to automotive and industrial machinery.
For now, ZNL Bearings remains committed to providing the best possible solutions for our clients, including high-quality bearings like deep groove ball bearings, tapered roller bearings, and angular contact bearings. As we continue to explore new technologies, we are confident that our ability to deliver reliable, high-performance bearings will only improve.
Conclusion
3D printing is undoubtedly a game changer for the bearing manufacturing industry, offering exciting possibilities for customization, cost savings, and material flexibility. While ZNL Bearings has not yet adopted this technology, we remain committed to exploring the future of manufacturing innovations to better serve our clients in the thermal power, agriculture, cement, and paper industries, among others.
Our focus remains on delivering top-quality bearing solutions, and as we monitor advancements in 3D printing, we will continue to provide our customers with the most reliable and customizable bearings available.